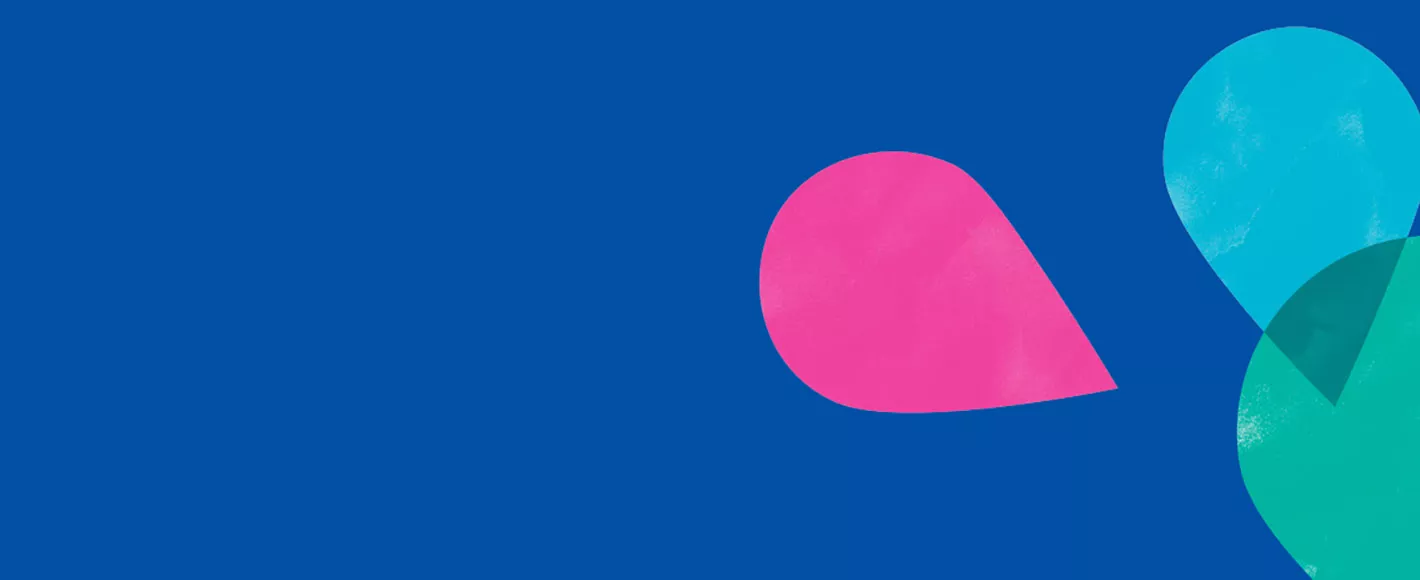
We’re committed to delivering crisp, clean tasting water, and we have high standards. That’s why every drop goes through a rigorous 13-step quality process.
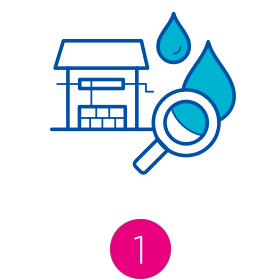
Source receiving
Sample is taken from Source daily and not weekly.
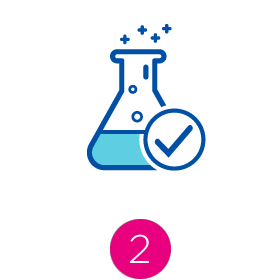
Pre-treatment
Pretreatment available with Stripping tank to adjust PH and Iron oxidation.
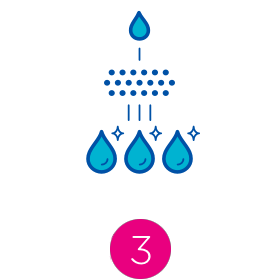
Sand filtration
For particles, Fe3+ removal and the nitrification process.
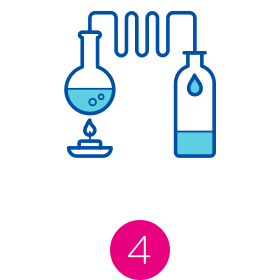
Demineralization process
Reverse osmosis-use of high pressure pump and special membranes called semi permeable memebranes to reverse the natural phenomenom of osmosis.
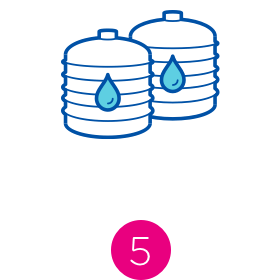
Water storage and monitoring
Water is received into storage tanks. Water carefully monitored daily.
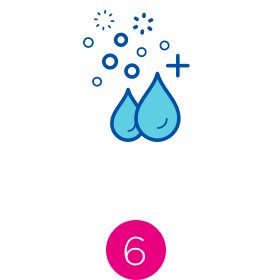
Remineralization
Minerals are added.
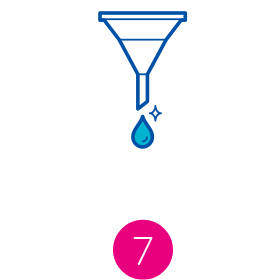
Micro filtration
Micro filters used for water filtration. These filters are pharmaceutical grade and are designed to remove particles as small as 0.2micron in diameter. Filtration process monitored hourly and tested daily.
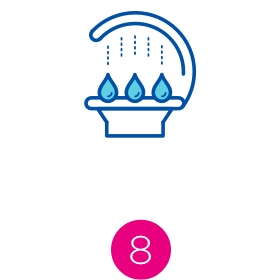
Ultra violet light disinfection
The combined effect of microfiltration and ultraviolet light provide added assurance of product disinfection and safety. Process continually monitored by instrumentation and checked/monitored hourly.
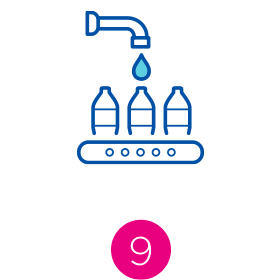
Bottling control
Bottling is conducted under very controlled conditions using state-of-the-art equipment. Each bottle is given a specific code that identifies the plant location and time produced. Process monitored and tested continuously. Filling room and environment are of high sanitary standards.

Packaging control
Packaging is conducted using the latest in modern equipment. Packaging materials not meeting internal standards are rejected. Bottles, caps and labels are carefully controlled and monitored by lot. PET preform are received from vendors and developed in blown bottles on-site for quality control.
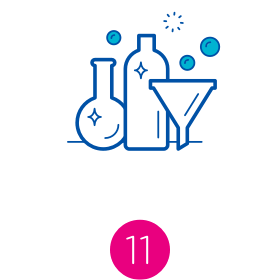
Cleaning-in-place sanitation process
Line sanitation practices include advanced internal pipe and equipment cleaning methods called C.I.P. This automated cleaning process recirculates cleaning chemical and sanitizing solutions at the precise temperatures and time to affect total control and maximum effectiveness of the line sanitation process.
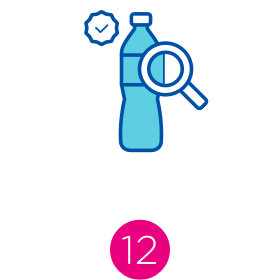
Plant quality control and HACCP program
The plant has a fully staffed Quality Assurance Department and laboratory that maintain the plant Quality Control Processes. Water, packaging materials and plant processes are carefully monitored to ensure they meet company specifications and standards. There is HACCP in place and CCPs and OPRPs are clearly identified, monitoried as defined in QMS and form part of release process.
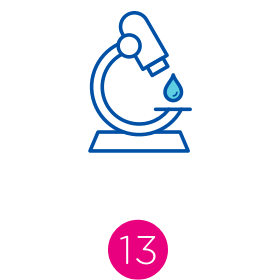
Corporate Quality Assurance Program
National Testing Laboratory is equipped with state-of-the-art testing machinery and staffed with degreed, experienced personnel. Comparative analyses are performed on poducts in accordance with State and Federal Regulatory standards. Independent from the Quality Control and Quality Assurance Departments, the corporate Quality Assurance Program sets company-wide standards, specifications and monitors plant quality programs.